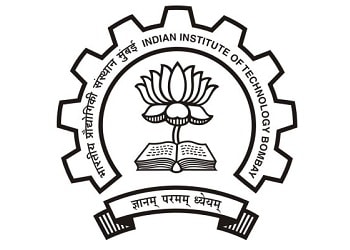
Researchers at the Indian Institute of Technology (IIT) Bombay have successfully made low-cost piezo-resistive vibration sensors using polyurethane foam coated with carbon nanomaterial-based ink.
These sensors can be used for monitoring the health of industrial machines and equipment and help identify incipient failures thereby enabling efficient maintenance schedule planning.
The ink is made of functionalised multi-walled nanotubes that are dispersed in a reduced graphene oxide matrix.
It is conductive due to the presence of large number of multiwalled nanotubes.
The ink, which uniformly coats the pores of the foam when dipped-coated, imparts piezo-resistive properties.
Conductive sheets (made of indium titanium oxide coated polyethylene teraphalate) were pasted on the top and bottom sides of the foam and electrical wires connected to the sheets for measurements.
The ink and sensor were developed at the Plastic Electronics and Energy Laboratory (PEEL), Department of Metallurgical Engineering and Material Science, IIT Bombay.
How It Works- When the PU foam coated with the ink is perturbed, in this case compressed, the air gaps are removed and the foam gets thinner.
- This provides a conduction path for electrical charges. The resistance drops as the foam is compressed and it becomes more conductive.
- The sensor is so sensitive that it can measure blood pulse.
- The total cost of materials required for making the sensors works out to less than Rs.200 per sensor, and can be reduced further if mass produced.
- The ink costs only about Rs.7 per sensor. No sophisticated equipment is required for fabricating the sensor.
- The sensing bandwidth of the sensor is 80 Hz and the team was able to classify different machine operating conditions (good versus bad bearing, and good versus bad gearbox) based on vibration signals.
- To be able to identify the danger signs of a machine, the output of the vibration sensor has to be captured and the Fast Fourier Transform (FFT) has to be computed. One should then look where the peaks are located in the FFT.